Anyway, I digress, as the real point of this story is to tell you about some places we're recently visited on class trips. We've visited a couple of distilleries of course. But thats not what I want to talk about. Distilleries are interesting, but they are usually open to the public. I'm going to talk about some locations that few people get to see: a copper smiths where they make the stills, a cooperage where they make the oak barrels, and a huge warehouse where they age the whisky. All three are out near Alloa, NW of Edinburgh on the edge of the highlands.
First, a little background story. All three locations are owned by Diageo, a company that produces many premium alcoholic beverage brands. As far as Scotch goes, they own 28 distilleries in Scotland (about 1/3). Talisker, Carol Ila, Glenkinchie, Lagavulin, and many other single malts are all part of their family. Most Scotch, however, is blended into brands such as J&B and Johnnie Walker (which they also own).
Diageo is quite supportive of the brewing & distilling program here, and have been very kind to give us tours of many of their sites. Diageo is quite well vertically integrated, owning all three places we visited. The first place was a copper smiths where we were quite privileged to see just how copper stills are made.
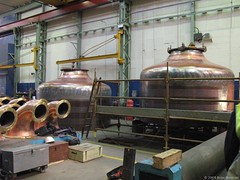
Copper smiths: two new stills! (Click any photo for a larger version!)
A still is, basically, a big boil kettle that evaporates alcohol then condenses the alcohol-rich vapour. Most Scottish malt distilleries use two stills... the first to strip the wash (beer at about 7-8% abv) of its alcohol and flavour compounds. This creates the low wines (a liquid of about 25% abv), which is then distilled in the second still to approximately 70% abv. Most stills are made of copper, which reacts with sulphur to remove it from the product. The result of this is that the stills need to be replaced every 10 years or so. The Abercrombie Copper smiths do just this for all of Diageo's distilleries.
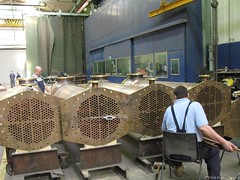
Putting together shell-and-tube condensers that will one day cool new spirit from vapour to liquid.
The construction of a still starts with the welding of copper plates together, followed sometimes by a machine hammering to get the basic shape. The final shape is all pounded in by hand, which is still the best way to do it as it turns out. Needless to say, the shop we visited was quite noisy! At the shop they were producing 14 new stills for a new distillery that will come online next year. Stills are designed to a very specific shape... a small change in design can change the final spirit character. They have to work to exacting specifications. It was very interesting to see where stills are born, it certainly looked like a lot of work.

Foreground: the bottom of a new still in production.
Oak barrels are another key to the whisky industry. By law, all Scotch has to be produced in Scotland and aged for at least three years in barrels less than 700 L in volume. Oak barrels come second-hand from two sources: the American whisky industry (bourbon), and Europe (wine/sherry/etc). A cooper is a highly skilled tradesman that can build these barrels, which consist of staves (thick wood strips) bent into shape and held together with metal rings. The nature of the wood and the compression between the staves results in a liquid-tight seal (although alcohol and water can evaporate through the cask over time).


1) Bunched staves as they arrive from overseas. 2) A cooper placing the staves back together to create the appropriate sized barrel.
The oak barrels are broken down into the staves, packed on a shipping skid, and shipped over to Scotland. The coopers here put them back together. In traditional cooperages this is all done by hand, but the location we visited was machine assisted (its still a really hard job though!). Casks are charred with a flame on the inside to release wood flavour compounds (and create a layer of carbon that will absorb undesirable compounds from the whisky).
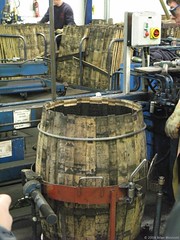

1) The cooper tightens the staves with a machine to place the upper hoop on. 2) casks are steamed to expand the wood, and charred for flavouring.

Inside a charred barrel.
Once the barrels are put back together, newly charred ones are sent off for "sherrying". Now I'll tell you, this is where one of the romantic 'myths' about Scotch that I had heard was refuted right in front of my eyes. The story goes that oak cask with sherry from Spain are shipped to Scotland, where the sherry is removed and bottled for consumption, and the barrels are used for Scotch maturation. Not so. They have a big tank of sherry... they fill the newly charred casks with sherry... they let it age for three months... then they empty the sherry back into the sherry tank (through a filter). They can use the same sherry batch for about 8 or 9 years. Yes, that is what they do.
Unfortunately, they don't allow you to take photos in any area that has ethanol floating around in the air, so you'll have to take my word for it (and lets face it, it makes more sense than shipping these casks all over the place).


1) A machine to help place the lid in the cask. 2) A machine to push down the metal rings that keeps the wood tight together.
The purpose of adding the sherry to the cask is a little bit different that I had thought, too. The main purpose of the sherry is to remove some character from a newly charred cask. Otherwise, the character of the wood would overpower the distillery character of the whisky over the maturation time. Apparently it doesn't add colour, that comes from the char and the wood.
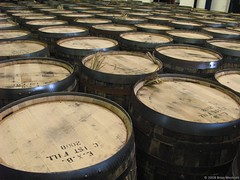
Finished casks!
Moving on, the third place we were privileged to see was the Blackgrange warehouse. Blackgrange houses about 3.5 million casks of whisky. In duty owed in taxes alone, its about 10 billion pounds sterling. Needless to say... its HUGE. They have very strict regulations too... you can't bring anything that could possibly contain liquid on site, you can't bring matches or lighters, nor cell phones, nor cameras. They are quite paranoid about any accident.
Anyway, there are three key parts to this operation. First, tanker trucks from carrying new make spirit from the distilleries arrive and their contents are pumped to vats. The new make spirit is diluted to usually 63% for aging to get the ideal flavour reactions with the oak wood. New make is horrid stuff, I wouldn't drink it. This is one reason you age for at least three years! The new make is then pumped into casks, sealed with a bung, and carted off to be placed in a massive warehouse. Every cask is bar coded... they know where every cask in that place is!
After aging, casks are brought out from storage and disgorged (emptied). This is done along a troph... simply take out the bung, stick an air tube in the hole (for faster emptying), and turn it upside down. This isn't a terribly sanitary operation, but nothing going to grow in a strong alcohol solution anyway! The whisky is pumped into a big tank, mixed with air for an hour or so, then pumped into tanker trucks. The trucks head off to the packaging facility, where the whisky is filtered, diluted to sales strength (usually 40-45% abv) and bottled!
I think I've rambled on about this enough for now; its hard to convey the enlightenment I've gained in the last few weeks into a small amount of space. If you want to see more photos you can check out my flickr set at http://www.flickr.com/photos/brianwestcott/sets/72157603996924944/
Cheers!
1 comment:
Hey Brian!
Great post. The guys at Abercrombie just finished a Pot Still for Glenkinchie. I wrote a post on it at http://www.whiskygrotto.com and linked back to this post for curious readers.
Thanks once again for this lenghty post.
/Johan
Post a Comment